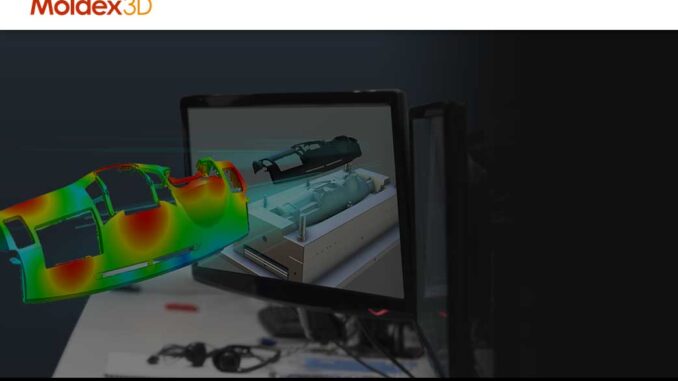
Czy dostępne są narzędzia, które usprawniają i automatyzują proces projektowy poprzez optymalizację analiz CAE w obszarze wtrysku tworzyw? Jedną z propozycji jest Moldex3D SYNC (Design Parameter Study)
Autor: Wayne Chang
Aby przeprowadzić jakąkolwiek analizę CAE na etapie projektowania produktu, należy wykonać szereg operacji. Najpierw inżynier-projektant powinien stworzyć model geometryczny 3D, a następnie wyeksportować gotowy plik z systemu CAD.
Następnie inżynier CAE wprowadza otrzymany plik modelu do oprogramowania CAE i uzupełnia ustawienia, takie jak chociażby warunki brzegowe, wybór materiału, generowanie siatki i warunki formowania itp. i dopiero wtedy może przeprowadzić analizę CAE. Po analizie musi jeszcze zinterpretować jej wyniki.
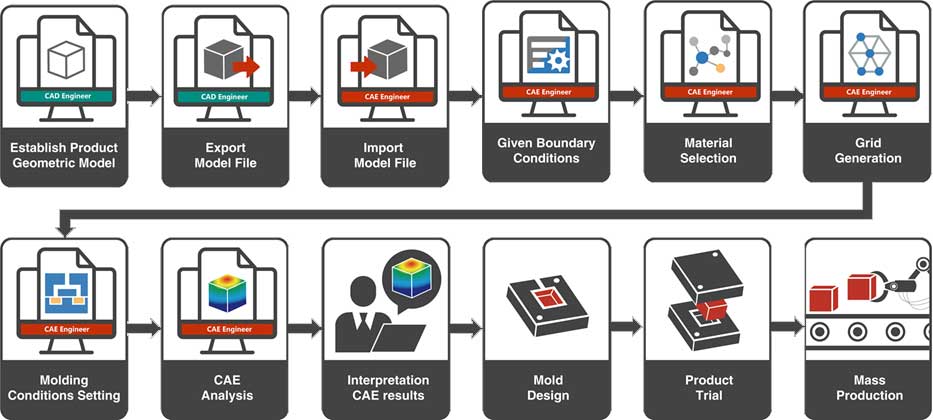
Jeśli interpretacja CAE wykaże, że w uzyskanej wyprasce są wady, należy wrócić do oprogramowania CAD, aby zmodyfikować model produktu, a następnie powtórzyć te same procesy, aż projekt zostanie zoptymalizowany pod kątem produkcji masowej. Gdy projekt zostanie zmieniony, cały przepływ pracy musi zostać powtórzony. Oznacza to powtórzenie m.in. wszystkich procesów przesyłania plików i przeprowadzania kalkulacji CAE, które pochłaniają dużo czasu i pracy.
Ponadto takiego przepływu pracy nie może wykonać sam inżynier CAD. Powodem jest to, że inżynierowie CAD mają możliwości edycji CAD, ale brakuje im doświadczenia z narzędziami do analizy i optymalizacji CAE.
Aby rozwiązać ten problem, Moldex3D opracował nową funkcję – badanie parametrów projektu (DPS – ang. Design Parameter Study) w programie Moldex3D SYNC, która umożliwia automatyczną analizę i pomaga użytkownikom szybko zakończyć cały proces analizy CAE.
Badanie parametrów projektowych Moldex3D SYNC (Design Parameter Study)
W procesie badania parametrów projektowych (DPS) do optymalizacji wymagany jest zestaw grup odniesienia. Po znalezieniu wyników, które należy poprawić, inżynierowie CAD mogą modyfikować parametry geometryczne lub tworzyć zupełnie nowe modele bezpośrednio za pomocą znanych sobie narzędzi do edycji geometrii CAD – aby zmieniać kształty geometryczne i rozmiary, które mogą wpływać na docelowe wyniki analizy.
Następnie użytkownicy mogą wybrać cechy geometryczne poprzez współczynniki kontrolne w DPS i ustawić górną i dolną granicę oraz wielkość zmiennych dla każdej cechy. W ten sposób określony zostaje pełny zakres dopuszczalnych zmian dla różnych kombinacji w projekcie. Każda kombinacja zawiera różne ustawienia kształtu i rozmiaru, a kombinacji może być kilkadziesiąt. DPS automatycznie wygeneruje odpowiednie geometrie 3D zgodnie z projektami o różnych rozmiarach. Po tym, jak geometrie przejdą kontrolę, kroki obejmujące generowanie siatki bryłowej, warunki brzegowe, materiał i ustawienia warunków formowania zostaną już wykonane automatycznie. Następnie rozpoczyna się analiza CAE, podczas której wykonywane są równoległe obliczenia dla różnych kombinacji projektowych – w celu skrócenia czasu oczekiwania na wyniki analizy CAE.
Po przeprowadzeniu analizy DPS podsumowuje wszystkie kombinacje parametrów projektowych i przedstawia wyniki analizy na wykresie. Projektanci produktów mogą przeglądać dane dotyczące formowania dla każdej kombinacji parametrów projektowych, aby znaleźć tą ich zdaniem najbardziej optymalną.
Jak to może wyglądać w praktyce?
W przypadku pokazanym na rys. 2 linia spoiny pojawia się w słabszej części wyrobu.
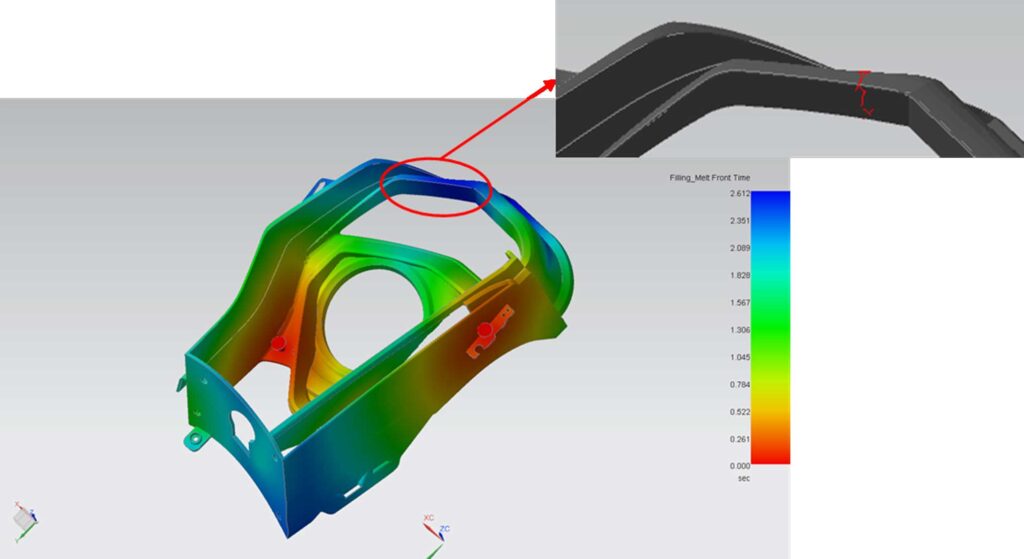
Zmieniając projekt produktu, możemy przesunąć pozycje linii spoin bliżej mocniejszych elementów konstrukcji. Najpierw używamy funkcji CAD, aby zmienić grubość części w określonych obszarach – i aby zmienić położenie linii spoiny (rys. 3).
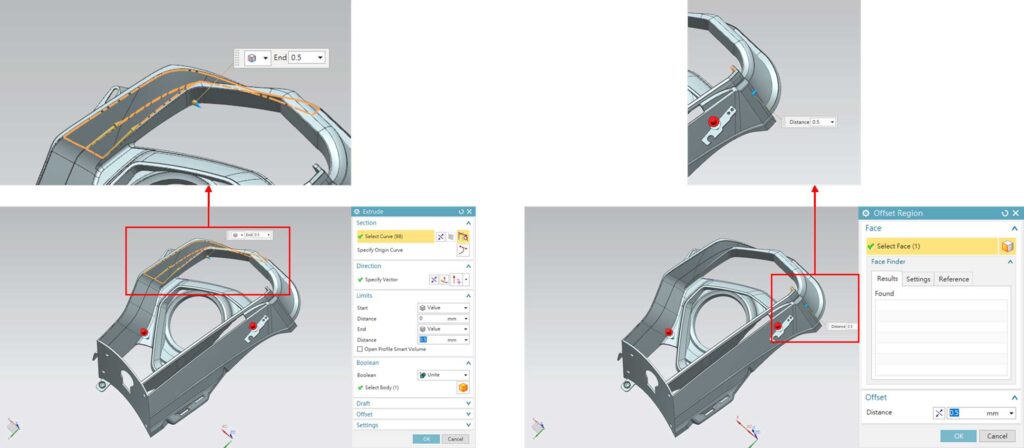
Użycie funkcji DPS pozwala zoptymalizować parametry zmiany grubości. Jako współczynnik kontroli wybieramy charakterystykę zmian grubości; dla współczynnika jakości wybieramy kontrolę przepływu wstecznego materiału, jak pokazano na rysunku 4. Teraz możemy sprawdzić, czy linie spoin pojawią się w określonych obszarach. Na koniec optymalizacja projektu jest przeprowadzana metodą pełnego projektowania czynnikowego.

Interpretacja wyniku
W wynikach analizy optymalizacyjnej możemy zobaczyć relacje między czynnikami sterującymi, a czynnikami jakości we wszystkich kombinacjach. Przedstawia to wykres parametrów (współrzędnych) równoległych (rys. 5) – widać kilka kombinacji ze 100% wynikami kontroli przepływu wstecznego.
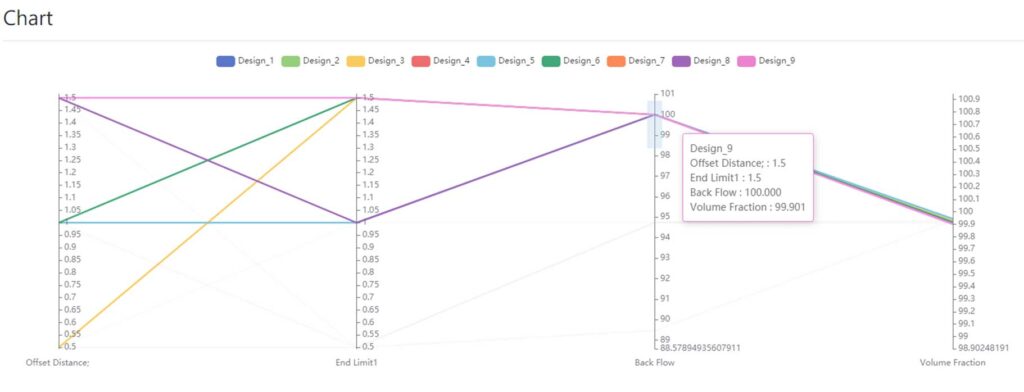
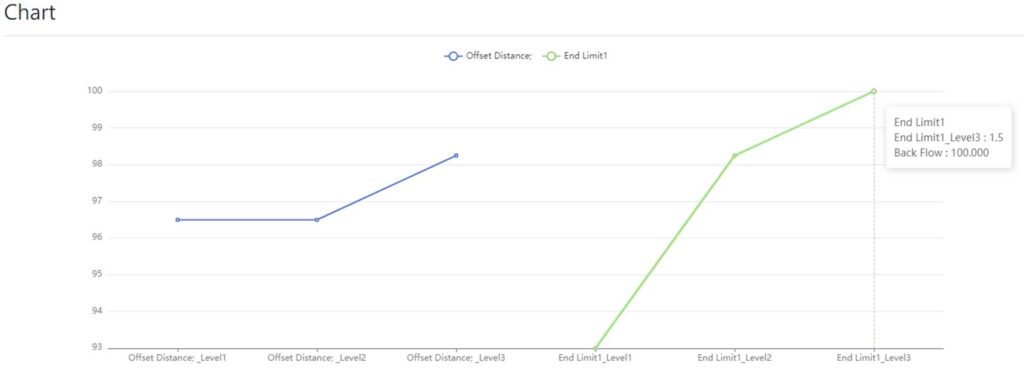
W połączeniu z wykresem odpowiedzi jakościowej (rys. 6) możemy zdecydować, która z kombinacji jest optymalna. Widać też, że im wyższy poziom współczynnika kontroli, tym wyższa będzie wartość kontroli przepływu wstecznego. W tym przypadku „Design_9” (rys. 5 i rys. 7) okazuje się projektem optymalnym.
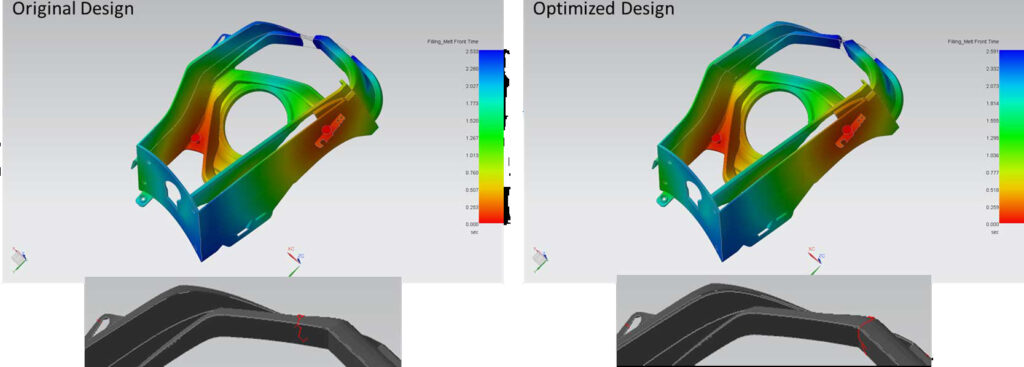
Więcej informacji o badaniu parametrów projektu (DPS)
Oprócz tego, że DPS jest już wbudowany w Moldex3D SYNC, trwa dalsza integracja z innymi systemami. Dzięki ich algorytmom i procesowi automatyzacji dostępnemu w CAE SYNC, użytkownicy będą mogli szybciej znaleźć optymalne parametry projektowe produktu.
Wayne Chang
Autor jest inżynierem w dziale badań i rozwoju produktów firmy CoreTech System (Moldex3D).
Bądź pierwszy, który skomentuje ten wpis