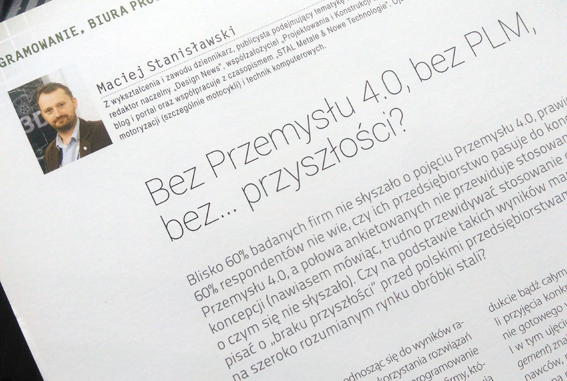
Blisko 60% badanych firm nie słyszało o pojęciu Przemysłu 4.0, prawie 60% respondentów nie wie, czy ich przedsiębiorstwo pasuje do koncepcji Przemysłu 4.0, a połowa ankietowanych nie przewiduje stosowania koncepcji przemysłu 4.0 (nawiasem mówiąc trudno przewidywać stosowanie czegoś, o czym się nie słyszało). Czy na podstawie takich wyników mam prawo pisać o „braku przyszłości” przed polskimi przedsiębiorstwami działającymi na szeroko rozumianym rynku obróbki stali?
Autor: Maciej Stanisławski
(Artykuł opublikowany w „Raport. Rynek obróbki stali w Polsce 2019”, wyd. Elamed)
Około pięć lat temu, odnosząc się do wyników raportu w odniesieniu do wykorzystania rozwiązań informatycznych (systemy CAD, oprogramowanie CNC, rozwiązania PLM), sugerowałem, by firmy, które modernizują swój park maszynowy, inwestują w profesjonalne centra obróbcze etc., rozważyły inwestycje w systemy zarządzającymi danymi o produkcie, bądź całym cyklem jego życia. Od chwili przyjęcia konkretnego zlecenia, po dostarczenie gotowego wyrobu dla końcowego odbiorcy. I w tym ujęciu PLM (ang. Product Lifecycle Management) znajduje zastosowanie także u podwykonawców, producentów elementów, komponentów na potrzeby innych producentów. Pozwolę sobie na cytat podsumowujący poprzedni komentowany przeze mnie raport: „(…) Dobrze dobrane i wdrożone PLM (…) pozwala zredukować koszty produkcji o 20-30% w skali roku (nie mówiąc o oszczędnościach związanych ze zminimalizowaniem np. ryzyka przerabiania/wykonywania nowych narzędzi, prototypów etc.). Warto być tego świadomym, zanim podejmie się decyzję o instalacji kolejnej maszyny CNC w swojej hali…”.
Bez nowoczesnych rozwiązań informatycznych – czy będzie to system ERP, czy PDM, czy PLM (dwa ostatnie z racji moich zainteresowań są mi zdecydowanie bliższe), czy jakikolwiek system informatyczny pozwalający na zarządzanie produktem/produkcją – nie ma co marzyć o „Industry 4.0”. Tymczasem okazuje się, że… „informatyczny system zarządzania produkcją” wdrożyło, bądź planuje to uczynić w najbliższym czasie niecałe 31% badanych przedsiębiorstw – vide tabela XV. 4, a „informatyczny system zarządzania przedsiębiorstwem” funkcjonuje (lub niedługo będzie funkcjonował) w ok. 30% firm zajmujących się obróbką stali – vide tabela XV. 5.
Usługi projektowe i konstrukcyjne świadczy w sumie nieco ponad 50% badanych firm, w tym prawie 12% na zasadach outsourcingu. Tabela XIII. 1. oprócz danych podstawowych zawiera również listę posiadanego przez respondentów oprogramowania 3D-CAD i 3D-CAM.
Zdecydowana większość (blisko 86%) firm świadczących usługi konstrukcyjno – projektowe jest w stanie wykonać projekt CAD/CAM na podstawie dokumentacji papierowej…
Najbardziej popularne typy oprogramowania: Solid Edge, SOLIDWORKS, Autocad, Inventor,
CATIA, NX, MasterCAM, Rino, Unigraphics, Autodesk, Esprit, inny CAD 3D…
To doskonale responduje z wynikami z innej ankiety, przytoczonymi już na wstępie. Te 30% firm, w których funkcjonują systemy IT wspomagające produkcję, to przedsiębiorstwa świadome wyzwań stawianych im przez „czwartą rewolucją przemysłową”. Liczyłem, że będzie ich połowa, te 30% to naprawdę niewiele.
I znowu: na etapie projektowania produktu, procesu lub technologii prawie 60% firm wykorzystuje narzędzia do symulacji komputerowej. To cieszy – chociaż w tej chwili takie narzędzia znajdziemy w większości popularnych systemów CAD 3D. Ale jednocześnie ponad 70% respondentów nie zna pojęcia rzeczywistości rozszerzonej, a dla ponad połowy pojęcie „Internetu rzeczy” (ang. IoT – Internet of things) nie jest znane! Gdzie zatem znajdziemy tutaj miejsce na „Przemysł 4.0”?
Widać u respondentów świadomość, że stopień zaawansowania systemu informatycznego w ich firmie jest na poziomie niskim. Mimo to 60% deklaruje, że obecny system informatyczny pozwala gromadzić dane produkcyjne, procesowe oraz eksploatacyjne. I jednocześnie 80% firm nie gromadzi, nie udostępnia oraz nie przetwarza danych w tzw. „chmurze”. Dlatego nie byłem specjalnie zdziwiony, gdy przeczytałem, że niespełna 13% firm stosuje drukarki 3D lub inne urządzenia do wytwarzania przyrostowego. Na tle innych wyników, to i tak całkiem sporo: oznacza, iż korzysta z nich blisko połowa tych firm, które korzystają z „informatycznych systemów zarządzania produkcją” i które jednocześnie wiedzą, czym jest „Przemysł 4.0”…
Co z tymi, którzy nie wiedzą?
Inwestycje w oprogramowanie? Po co?
Na niezbyt szczęśliwie sformułowane pytanie: „czy firma planuje w najbliższym roku inwestycje w park maszynowy – jeśli TAK – zakup jakich maszyn/urządzeń/oprogramowania (wyróżnienie autora) jest planowany?” nieco ponad 5% respondentów odpowiedziało, że planuje zakup oprogramowania do „analizy produkcji”, a oprogramowanie CNC i przeznaczone stricte do projektowania zakupi niespełna 2 procent. Inni tego nie planują? Pocieszam się, że może nie chcieli deklarować tego w ankietach. Do czego zmierzam?
Ok. 72% firm posiadających maszyny CNC korzysta zarówno z oprogramowania, jak i sterowników pochodzących od ich producentów. Blisko 26% korzysta z dostawców niezależnych…
Termin Industry 4.0 został po raz pierwszy użyty w 2011 roku (przewiduje się, że urzeczywistnienie tej wizji może zająć 10-20 lat, także wpisanie jej w 25-letni plan rozwoju jest całkiem sensowne).
– Industry 4.0 (polski „Przemysł 4.0”) jest wizją rozwoju przemysłu i produkcji w Niemczech, która została opracowana na podstawie badań porównawczych konkurencyjności gospodarki niemieckiej zleconych przez niemiecki rząd federalny – wyjaśniał w 2014 roku Mariusz Zabielski, prezes Siemens Industry Software, w rozmowie z dziennikarzami portalu gospodarczego wnp.pl.
„Czwarta rewolucja” będzie wykorzystywała cyfrowe modele produktów, które będą powstawały w dużej zgodności z wymaganiami klientów, a następnie będą wytwarzane w inteligentnych fabrykach (Smart Factory) charakteryzujących się dużą elastycznością, niezawodnością i wydajnością – opisywał przedstawiciel Siemens Industry Software. – Składnikami inteligentnych fabryk będą elementy zwane systemami cyber-fizycznymi, które współpracując ze sobą będą określały i realizowały optymalną metodę wytwarzania i dostarczenia produktu do klienta…
Jeśli nie będziemy tego świadomi, nie zdecydujemy się na inwestycje w „narzędzia” – nie tylko do obróbki skrawaniem, ale – do wspomagania procesów projektowych, produkcyjnych i pozwalających na lepsze zarządzanie całością przedsiębiorstwa, to przyszłość – szczególnie przed tymi 50-70% „nie zorientowanych” – nie rysuje się w różowych barwach. Z drugiej strony ta blisko trzecia część „świadomych” ma szansę na dynamiczny rozwój i szybkie zagospodarowanie rynku. Potrzebne po temu rozwiązania mają w zasięgu ręki…
(ms)
• link do pełnej wersji Raportu można znaleźć na stronie wydawnictwa ELAMED (link tutaj)
Internet rzeczy (również Internet przedmiotów, ang. Internet of Things – IoT) to koncepcja, wedle której jednoznacznie identyfikowalne przedmioty mogą pośrednio albo bezpośrednio gromadzić, przetwarzać lub wymieniać dane za pośrednictwem np. sieci komputerowej, odpowiedniego systemu komputerowego etc. Do tego typu przedmiotów zaliczają się między innymi urządzenia gospodarstwa domowego, artykuły oświetleniowe i grzewcze, ale także (a może przede wszystkim –przyp. autora) maszyny produkcyjne, roboty przemysłowe i inne. Podstawowym celem Internetu rzeczy jest stworzenie inteligentnych przestrzeni tj. inteligentnych miast, transportu, produktów, budynków, systemów energetycznych, systemów zdrowia czy innych związanych z życiem codziennym. Zastosowania Internetu rzeczy w przemyśle obejmują inteligentne maszyny, które wyposażone w zestaw czujników same „wiedzą”, w jakim są stanie i kiedy poszczególne podzespoły wymagają konserwacji czy wymiany.
Bądź pierwszy, który skomentuje ten wpis